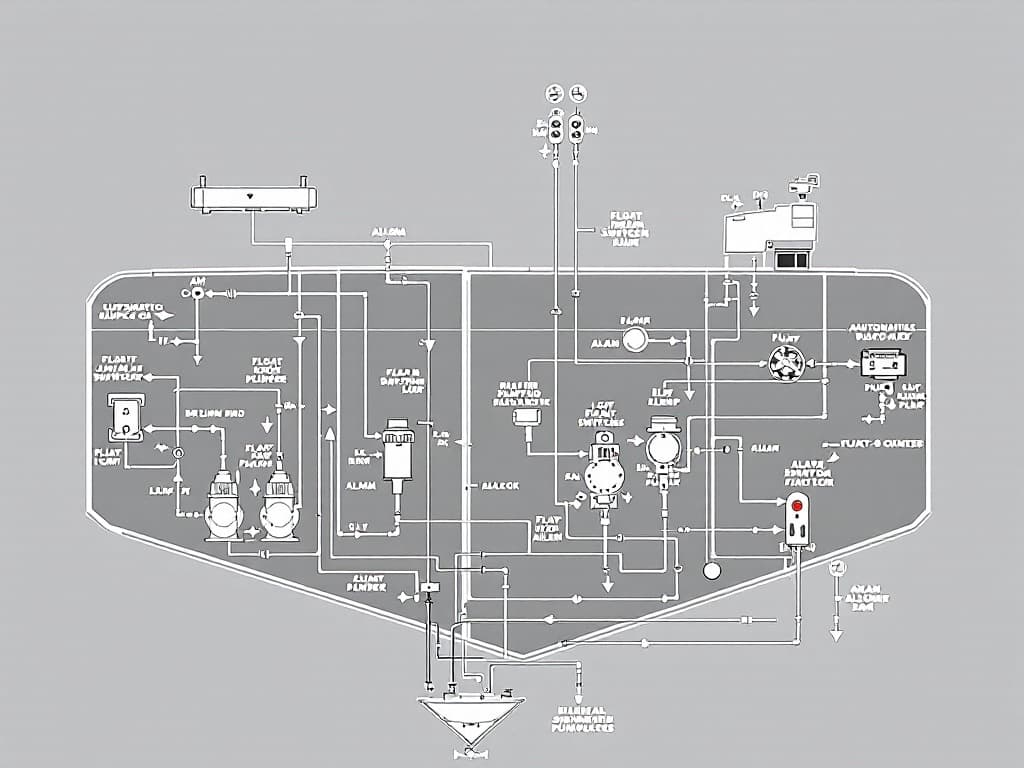
YACHT BILGE SYSTEMS: COMPREHENSIVE GUIDE
- Bilge Pump Systems
Primary Pumps:
- Electric submersible pumps for small vessels (under 40ft) range from 500-2000 GPH, with costs between $150-400 per unit. These pumps typically require 12V or 24V DC power systems and should be connected to dedicated circuit breakers. Installation costs add $200-300 per pump, including proper wiring, hose connections, and testing
- Heavy-duty electric pumps for mid-size vessels (40-80ft) deliver 2000-4000 GPH, with prices ranging from $400-800 per unit. These systems often feature dual voltage capabilities and advanced float switch mechanisms. Professional installation adds $400-600 per pump, including proper mounting brackets, anti-vibration pads, and electrical connections
- High-capacity pumps for large vessels (over 80ft) start at 4000 GPH and can reach 8000+ GPH, costing $800-2000 per unit. These commercial-grade pumps often feature bronze or stainless steel construction and sophisticated control systems. Installation costs range from $800-1500, requiring specialized expertise and often custom mounting solutions
Backup Systems:
- Manual bilge pumps, required by safety regulations, range from $100-300 for basic units. These must be accessible from the deck and capable of operation when electrical systems fail. Installation requires careful planning for optimal lever placement and efficient operation
- Secondary electric pumps should operate on independent power sources, typically costing $300-600 plus installation. These systems should be positioned at slightly higher levels than primary pumps and include separate float switches and control panels
- Emergency portable pumps should be stored in easily accessible locations, with costs ranging from $200-500 for marine-grade units. These should include sufficient discharge hose length and multiple power connection options
- Monitoring Systems
Electronic Monitoring:
- Basic float switches ($30-80 per unit) require monthly testing and annual replacement. These should be mounted with proper consideration for vessel movement and include secondary high-water alarms. Installation must account for proper switch activation angles and reliable wire connections
- Advanced electronic monitoring systems ($500-2000) offer multiple zone monitoring with LCD displays at helm stations. These systems typically include data logging capabilities and can integrate with vessel management systems. Installation requires proper network integration and sensor placement throughout the vessel
- High-end systems with smartphone integration ($2000-5000) provide real-time alerts and remote monitoring capabilities. These systems often include video monitoring of bilge spaces and can track pump cycling patterns. Professional installation includes proper calibration, network security setup, and crew training
- Plumbing Components
Essential Hardware:
- Marine-grade hoses cost $8-15 per foot, requiring careful routing to prevent water traps and ensure proper flow. All connections must be double-clamped with stainless steel clamps, and hoses should be properly supported every 18-24 inches
- Through-hull fittings range from $50-150 each, requiring professional installation with proper backing plates and sealants. These fittings should be bronze or composite construction with ball valves for emergency closure. Regular inspection and operation of valves is essential
- Check valves and strainers ($40-100 per unit) prevent backflow and protect pumps from debris. Installation must consider accessibility for cleaning and maintenance. Regular inspection of check valve operation is crucial for system reliability
- Maintenance Requirements
Regular Service:
- Monthly testing protocols must include operation of all pumps under load conditions, verification of float switch operation, and inspection of all visible plumbing connections. Documentation of these tests should be maintained in the vessel's maintenance log and include pump cycling times and current draw measurements
- Quarterly maintenance involves complete cleaning of all strainers, inspection of electrical connections for corrosion, and testing of high-water alarms. This should include removal and cleaning of float switches, verification of anti-siphon loop integrity, and testing of manual override systems
- Annual service requirements include replacement of pump impellers, inspection of all hose connections, and complete system flow testing. Electrical systems should be thermally scanned for potential issues, and all ground connections should be verified and cleaned
- Emergency Systems
Backup Equipment:
- High-volume portable pumps for emergency use ($500-1000) should include both electric and hydraulic options. These units should be tested monthly and maintained in ready-to-deploy status with all necessary hoses and power connections. Crew training must include proper deployment and operation procedures
- Battery backup systems ($300-800) should provide minimum 24-hour operation of primary pumps. Installation must include proper charging systems and automatic switchover capabilities. Regular testing under load conditions is essential for reliability
- Generator tie-in systems ($1000-2500) provide extended operation capability during power failures. These systems should include automatic transfer switches and proper load management controls. Installation requires careful integration with vessel's electrical system
- Advanced Automation Systems
Control Integration:
- PLC-based control systems ($3,000-8,000) provide sophisticated pump management and monitoring capabilities. These systems can manage multiple pump zones with variable speed control and efficient power management
- Touch-screen interfaces ($1,500-4,000) offer intuitive control and status monitoring from multiple locations. System programming should include logical pump sequencing and failure mode operations
- Data logging capabilities record all pump operations, alarms, and system changes for future analysis. This information can be used for predictive maintenance and troubleshooting
- Environmental Compliance
Regulatory Requirements:
- Oil-water separation systems ($5,000-15,000) are required for vessels over certain sizes. These systems must meet international standards for discharge water quality and include proper monitoring equipment
- Holding tank integration must prevent accidental discharge in restricted waters. Control systems should include geographic position monitoring for automatic operation mode changes
- Documentation systems must maintain records of all discharges and system operations for compliance verification
- Installation Best Practices
Professional Standards:
- All electrical connections must be made with marine-grade tinned wire, properly sized for maximum current draw plus 20% safety margin. Connections should be sealed against moisture and properly supported
- Hose runs should minimize bends and rises, with proper support every 18-24 inches. Anti-chafe protection must be installed where hoses pass through bulkheads or near moving parts
- Pump mounting requires proper isolation from hull structure to minimize noise transmission. Mounting locations must consider maintenance access and emergency manual operation
- System Integration
Vessel Management:
- Integration with main vessel monitoring systems should include redundant communication paths and fail-safe operation modes
- Remote monitoring capabilities must include proper security measures to prevent unauthorized access
- Alarm systems should prioritize notifications based on severity and provide clear instruction for crew response
- Future Technologies
Emerging Solutions:
- AI-powered pump management systems can learn normal bilge water patterns and predict potential issues
- IoT sensors provide enhanced monitoring capabilities with predictive maintenance alerts
- Advanced filtration systems reduce environmental impact and extend pump life through improved debris handling

Friendly & suitable opinions

Quality work done faster
